Advanced Welding WPS: Tailoring Specs for Facility Projects
Achieving Welding Quality: Revealing the Tricks of WPS Implementation and Optimization
In the world of welding, accomplishing quality is a pursuit that rests on the precise implementation and optimization of Welding Treatment Specifications (WPS) These fundamental documents act as the backbone of welding operations, dictating the procedures and parameters necessary for creating high-quality welds constantly. Nonetheless, the secrets to unlocking the complete possibility of WPS lie not just in recognizing its importance but additionally in understanding the complexities of its implementation and optimization. By diving right into the crucial elements, methods, obstacles, and finest methods linked with WPS, a world of welding quality awaits those who are willing to explore its depths.
Importance of WPS in Welding
The Importance of Welding Treatment Requirements (WPS) in the welding sector can not be overemphasized, acting as the backbone for making sure uniformity, quality, and security in welding operations. A WPS gives comprehensive guidelines on how welding is to be accomplished, consisting of important variables such as materials, welding procedures, joint style, filler metals, interpass and preheat temperatures, welding currents, voltages, traveling rates, and a lot more. By sticking to a well-defined WPS, welders can preserve harmony in their work, bring about regular weld high quality across various jobs.
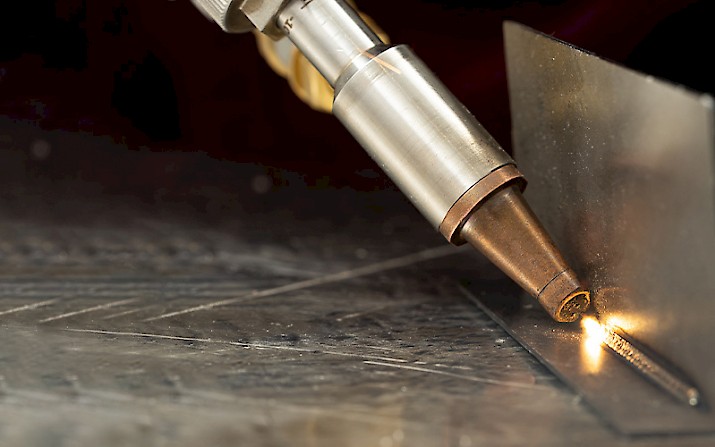
Crucial Element of WPS
Talking about the essential elements of a welding treatment specification (WPS) is crucial for comprehending its function in welding operations. An extensive WPS consists of a number of crucial elements that assist welders in accomplishing top quality and consistency in their work. One essential facet of a WPS is the welding process spec, which describes the particular welding processes to be used, such as gas tungsten arc welding (GTAW) or secured steel arc welding (SMAW) In addition, the WPS consists of information on the welding products, such as the kind and specs of the base steel and filler metal to be utilized. The WPS additionally specifies important variables like welding specifications, interpass and preheat temperature requirements, and post-weld heat therapy procedures. In addition, it includes info on joint style, fit-up, and any kind of unique strategies or preventative measures necessary for the welding operation. By including these essential elements right into the WPS, welding procedures can be standard, guaranteeing high quality, efficiency, and security in welding procedures.
Techniques for WPS Optimization
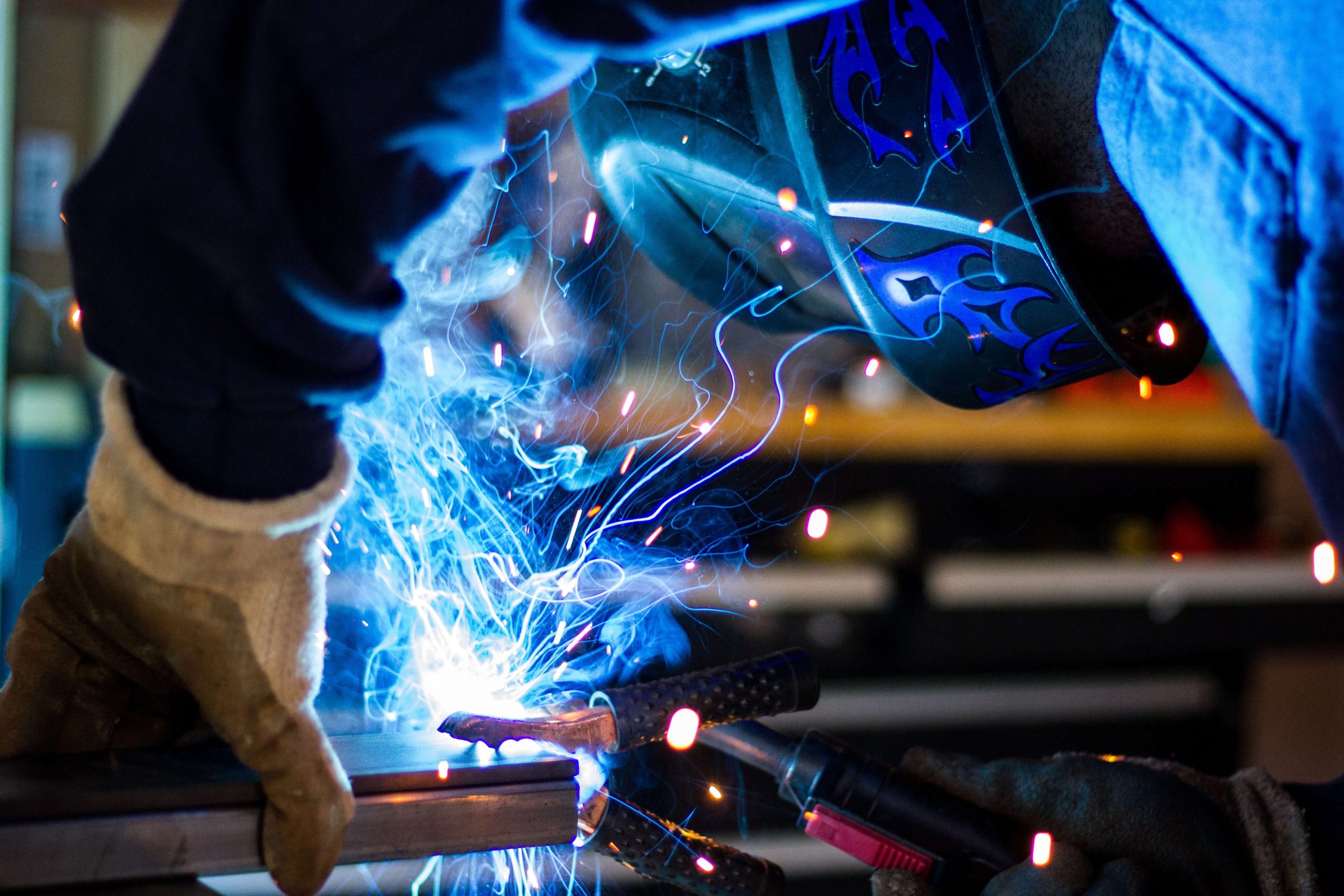
Secondly, training and qualification of welding personnel according to the specific needs of the WPS is paramount. Giving thorough training programs and ensuring that welders are licensed to perform procedures detailed in the WPS can bring about greater quality welds and reduced rework.
In addition, leveraging technology such as welding software application and monitoring systems can aid in enhancing WPS. These tools can aid in tracking variables, making sure specifications are within specified restrictions, and providing other real-time responses to welders, enabling them to make instant modifications for enhanced weld high quality.
Typical Difficulties and Solutions
Encountering barriers in executing the techniques for WPS optimization can hinder welding procedures' efficiency and quality. One common challenge is poor training or understanding of the welding procedure specifications (WPS) amongst the welding team. This can cause incorrect implementation of welds, causing issues and rework. To address this, detailed training programs must be implemented to ensure that all welders are competent in analyzing and using WPS properly.
One more difficulty is the lack of proper documentation and record-keeping, which is necessary for WPS optimization. Without clear records of welding parameters, products utilized, and examination outcomes, it comes to be tough to identify locations for improvement and make sure consistency in welding procedures. Carrying out a robust documentation system, such as electronic welding administration software application, can aid enhance record-keeping and promote data analysis for continuous renovation.
Furthermore, irregular welding equipment calibration and upkeep can pose a significant difficulty to WPS optimization. Regular tools checks, calibration, and maintenance routines should be stuck to purely to ensure that welding criteria are properly managed and preserved within the specified resistances (welding check that WPS). By attending to these common challenges with aggressive services, welding procedures can boost efficiency, high quality, and overall his explanation welding quality
Best Practices for WPS Implementation
To ensure effective WPS implementation in welding operations, adherence to sector requirements and precise focus to information are paramount. When starting WPS execution, it is critical to begin by completely comprehending the particular welding demands of the project. This involves a thorough review of the welding treatment specifications, products to be bonded, and the environmental problems in which the welding will certainly occur.
When the demands are clear, the next step is to choose the ideal welding treatment that straightens with these requirements. This entails speaking with the appropriate codes and criteria, such as those given by the American Welding Society (AWS) or the International Organization for Standardization (ISO), to make sure conformity and top quality.
Moreover, recording the entire WPS application procedure is vital for traceability and quality assurance. Comprehensive documents must be maintained regarding welding parameters, material prep work, interpass and preheat temperatures, welding consumables utilized, and any kind of variances from the initial treatment. Normal audits and testimonials of the WPS can aid identify areas for improvement and make sure continuous optimization of the welding procedure.
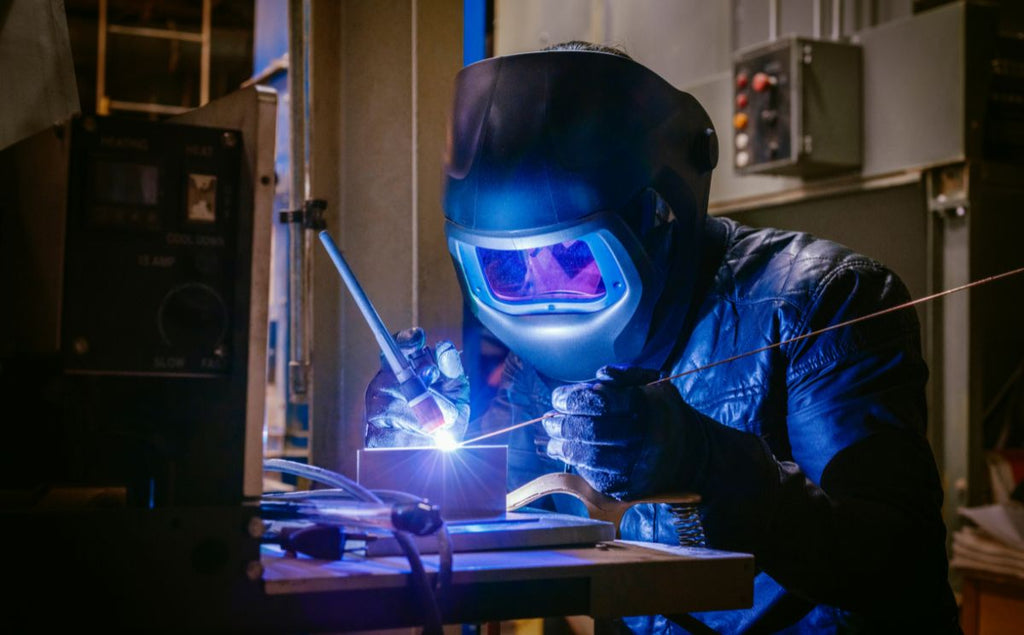

Conclusion
To conclude, the implementation and optimization of Welding Procedure Requirements (WPS) is essential for attaining welding quality. By comprehending the crucial elements of WPS, executing effective methods for optimization, addressing usual difficulties, and complying with ideal practices, welders can ensure premium welds and secure working conditions. It is imperative for specialists in the welding industry to focus on the appropriate implementation of WPS to improve overall welding efficiency and accomplish wanted results.
The Importance of Welding Procedure Requirements (WPS) in the welding industry can not be overstated, serving as the foundation for making certain consistency, top quality, and safety and security in welding procedures. A WPS supplies comprehensive directions on just how welding is to be brought out, including important variables such as products, welding processes, joint style, filler steels, interpass and preheat temperatures, welding currents, voltages, traveling speeds, and much more. One crucial element of a WPS is the welding procedure requirements, which outlines the certain welding procedures to be made use of, such as gas tungsten arc welding (GTAW) or protected steel arc welding (SMAW) By incorporating these vital elements right into the WPS, welding procedures can be standard, ensuring high quality, effectiveness, and security in welding operations.
It is crucial for experts in the welding sector to focus on the appropriate execution of WPS to enhance general welding efficiency and accomplish desired results.